GRは自らのブランドを「モータースポーツのDNAを継承するスポーツカーブランド」と定義する。まずはその出発点から話を始めよう。
大前提を取り戻すための「もっといいクルマづくり」
豊田章男会長が主導してきた「モータースポーツを起点としたもっといいクルマづくり」という言葉を検索してみると、最も古い使用例は2012年3月のこと。その後しばらくは、GR関係者が使う期間を経て、2016年にTOYOTA GAZOO Racingの公式サイトで使われるようになり、現在に至る。
豊田氏が社長に就任した時、トヨタはリーマンショックの影響で、4600億円の営業赤字に沈んでいた。豊田社長はそこで「もっといいクルマづくり」を掲げて、製品改革に取り組んだのだ。2001年からそれまでのトヨタは、毎年50万台のペースで販売を伸ばし、クルマを作れば売れる状態だった。
そういう状況では、生産速度の向上こそが必勝パターン。生産部隊の立場が強くなり、生産性の向上が至上命題になった。売れるから作るということ自体は間違っていないのだが、問題は作りやすさや速く作れることが、他の価値を押しのけて暴走を始めたことである。
当時のトヨタは、スポット溶接の数をより減らした設計者が高い評価を受けるというくらいまで歪み始めていた。人事評価の指標がそうなれば、その勢いは止まらなくなる。その結果、本来大事にすべきクルマの性能が犠牲になっていった。カスタマー向け、つまりB to Cの製造業にとって最も重要なことは製品が良いことである。それがおかしくなっていた。
トヨタには世界に冠たる「トヨタ生産方式」があり、より合理的な生産方法によって原価低減することが正しいという文化が今でもある。しかし、生産性の向上には本来大前提があったのだ。それは「いいクルマをつくる」ことだ。この時のトヨタはその大前提まで犠牲にしてコストダウンを進めてしまった。生産性向上の過剰な競争がそういう言うまでもない大前提を破壊した。
豊田社長はこれに危機感を感じ、「もっといいクルマづくり」を提唱した。その結果が今のトヨタの躍進へとつながったわけだが、果たして「もっといいクルマ」とはなんだろうか。加速が速いとか、燃費がいいとか、使い勝手が優れているとか、耐久性が高いとか。いいクルマの定義は無数にあり、何かひとつの指標に絞れない。
だからこそ豊田社長は、定量的な評価については一切口に出さず、ただ「もっといいクルマ」を繰り返した。その心は「今自分が作っているクルマのユーザーにとって、何がいいクルマなのかは自分で考えなさい」ということだった。
モータースポーツから量産へノウハウを転化
トヨタの社員ひとりひとりが真剣に考えて、いいクルマとは何かを模索し、形にしていった。しかし、実はもっといいクルマをつくるための、アイディアが膨大に集積されている場所があったのである。それはレースの現場だった。
レースの目的が勝利である以上、速く、安全に、正確に走り、しかも耐久性が高くなければならない。そうした性能向上を実現するため長年にわたって積み上げた膨大なノウハウは、豊田社長から見ても、確実にクルマをよりよいものに仕上げる具体的方法の宝庫だった。しかしそれらのノウハウは、手作り的手法で手間暇がかかるものであり、とてつもないコストがかかった。「競技の世界ではそうかもしれないけれど、とてもじゃないが生産車には採用できない」そう思われてきた。そのため量産車とは全く別の世界だとされて、長い間競技の世界だけで共有されてきた。
そこに目を付けたのが豊田社長である。そこに膨大なもっといいクルマづくりのためのノウハウがあるならば、使わない手はない。そこでトヨタはそういうモータースポーツの世界で確立された、いいクルマづくりのノウハウを量産に転化することを考えた。例を挙げ出せばキリがないほどある。例えばスポット溶接の増し打ち。あるいは構造用接着剤の併用。タイヤを接地させて1Gの重力をかけた状態での組み立て。部品の選別組み付け。足回り部品の静止状態での組み付けと言った具合である
こうした手法を取ることでこれまでモータースポーツの世界だけで活用されてきたもっといいクルマづくりのノウハウが、従来価格を大幅に下回る価格で製品化された。例えばワンオフに近い競技車両の代表を「GT3カテゴリー」だとすれば3000万円程度。対してGRヤリスは500万円程度で、しかも誰でも普通に購入できる。
つまりGRが開いた道は、競技車を扱う専門店でオーダーメイドで作られてきた特注車両をメーカーのカタログモデルに加えて、数分の1の価格で販売するという新しい世界だったのだ。
通常1分のサイクルタイムを約9分半に
では、それを一体どうやっているのだろうか。トヨタの場合、国内14の製造拠点のほとんどが、車種専用ラインで、1ライン1車種なのだが、1工場だけ例外がある。それが元町工場である。ここではライン1本を占有するほどには量産しないクルマのための混流生産ラインや、ハンドメイドの『センチュリー』をつくる特別な工場になっている。GRファクトリーもここの一角に置かれている。
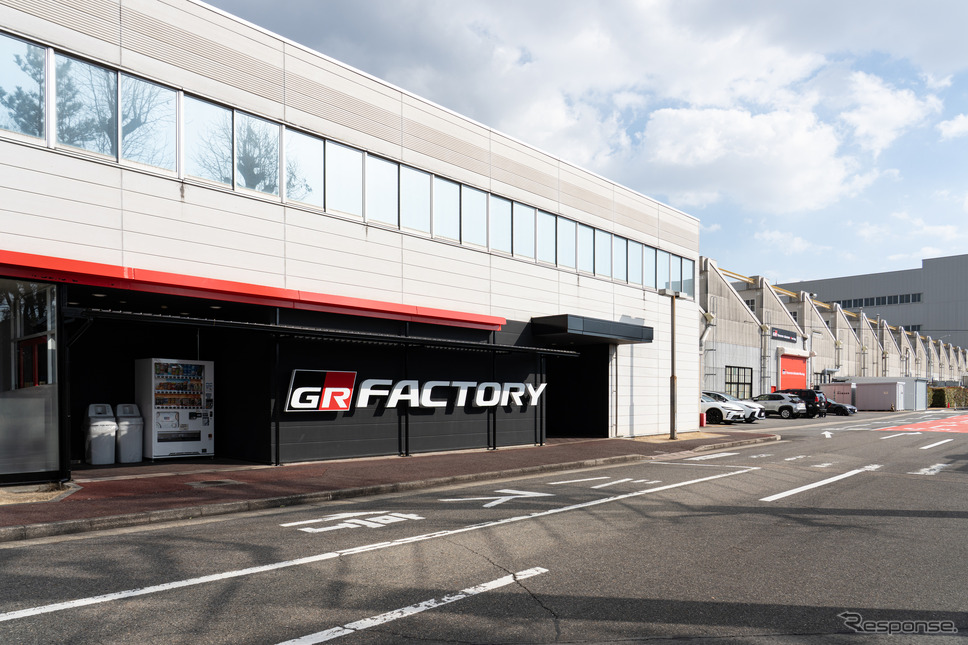
通常、トヨタの工場でのサイクルタイムは1分だ。流れ作業の工程は当然数珠繋ぎになっており、どの工程も必ず同じ時間で作業を終えなくてはならない。行進と同じで速度が揃っていなければ、前の人にぶつかるか、列の間隔が開いて問題が発生する。
なお一般にはタクトタイムと誤用されているがタクトタイムとはクルマ1台を作るのに何分かかっているかであり、生産効率を表すもの。1工程が何分で完了するかはサイクルタイムと呼ぶのが正しい。
さて、通常1分で完了するサイクルタイムを、GRファクトリーでは約9分半で回している。それはつまり、旧来は競技車をつくるショップの職人が手作りで対応していたものをラインに落とし込むためのコスト上昇と考えることもできる。逆に考えれば、世界中の量産メーカーが手を出せない領域の高性能車を9分半にすることで実現したということでもある。
それがトヨタにもたらすものは、熱狂的なファンと、トヨタの技術に対するリスペクトであり、それでトヨタが得るものはブランド価値の向上だ。